Depuis des dizaines d’années, nous concevons des sondes sur mesure afin de fournir des solutions qui répondent aux exigences uniques de nos clients. Aujourd'hui, nous sommes en mesure de tester les sondes que nous concevons directement sur les installations de nos clients en vue de garantir que les solutions d’inspection que nous proposons répondent bien à leurs besoins.
Ce type de conception hautement spécialisée doit souvent s’adapter aux exigences d’inspections commerciales et militaires critiques et exige confidentialité et expertise. Notre équipe d’experts regroupe des spécialistes de produits qui développent des solutions adaptées à des applications complexes, et des ingénieurs de développement réunissant plus de 100 ans d’expérience combinée dans le domaine.
Notre équipe se spécialise dans le développement de solutions intégrant des technologies de pointe : par ultrasons conventionnels (UT), par ultrasons multiéléments (PA), par courants de Foucault (EC) et par vibrations acoustiques. Nous aidons des clients de toutes les industries : production d’énergie, pétrole et gaz, transport (automobile, ferroviaire, aérospatial) et fabrication.
À ce jour, notre équipe a développé et fabriqué 25 000 sondes sur mesure à l’aide d’une variété d’outils de pointe, notamment les suivants :
- Tours CNC
- Impression 3D/fabrication additive
- Bras de mesure FaroArm®
- Logiciel de simulation CIVA NDT
- Sans oublier notre gamme complète d’appareils de recherche de défauts et d’appareils pour l’inspection des matériaux composites.
Relever le défi des applications d’inspection complexes
Généralement, les clients nous contactent pour obtenir une solution sur mesure après avoir essayé des solutions de remplacement courantes qui n’ont pas donné les résultats escomptés. Ils ont besoin d’aide pour contourner certaines restrictions, comme les contraintes d’espace et de taille, la géométrie complexe de certaines pièces, les matériaux difficiles à inspecter, les durées d’inspection restreintes et les exigences rigoureuses en matière d’imagerie et de dimensionnement.
Un projet de conception d’équipement sur mesure débute à l’instant où un client nous contacte pour nous exposer son problème. Au besoin, pour appuyer notre processus de développement, nous lui demandons de nous envoyer des échantillons de test et les renseignements requis sur les défauts. Nos experts effectuent d’abord des tests approfondis sur ces échantillons à l’aide de la technologie existante pour bien comprendre ce qui est requis pour résoudre l’application. Ensuite, ils travaillent au développement d’une solution en collaboration avec le client, tout en respectant les limites des exigences d’inspection de ce dernier. Ce processus inclut des recommandations concernant la sonde, l’outillage, le scanner ou l’appareil appropriés et, éventuellement, la présentation d’une solution développée sur mesure. Le client reçoit un rapport de test et un suivi en personne ou virtuellement.
Composer avec les restrictions qu’impose la COVID-19
Dans le contexte de la crise sanitaire entourant la COVID-19, nous organisons des démonstrations virtuelles en direct de nos solutions. Nous prévoyons maintenir ce service pour accommoder nos clients, lesquels peuvent aussi participer à une présentation en direct de nos appareils et même assister à l’inspection de pièces à partir de plateformes de partage communes (Microsoft Teams, Skype for Business, WebEx et TeamViewer). Nous prenons la sécurité très au sérieux, raison pour laquelle nous proposons un protocole de contrôle de transmissions (« Transmission Control Protocol », ou TCP) pour le traitement des renseignements liés au règlement sur le trafic international des armes (International Traffic in Arms Regulations, ou ITAR). Cela comprend un système de courrier électronique crypté et des solutions Microsoft pour une collaboration en toute sécurité avec les clients.
Du plus courant au plus spécialisé : des innovations axées sur les défis
Saviez-vous que notre sonde multiélément flexible standard a vu le jour à la suite d’une demande de conception d’une solution sur mesure ? Bien qu’il soit dorénavant courant de les utiliser pour l’inspection de coudes de tuyaux, le point de départ de leur développement a été marqué par une demande d’un client ayant besoin d’une sonde multiélément capable de s’adapter aux différentes géométries des composants aérospatiaux faits de polymère renforcé de fibres de carbone (CFRP).
Relever le défi de l’inspection des pièces à géométrie complexe
Il est difficile d’effectuer une inspection par ultrasons à haute résolution sur des pièces complexes présentant des géométries changeantes. Pour inspecter ce type de composants, les sondes à ultrasons conventionnelles doivent être placées perpendiculairement à la surface à tous les points d’acquisition des données. Ce processus d’inspection plus lent est susceptible de faire rater des défauts entre les points d’acquisition. La technologie PAUT (« Phased Array Ultrasonic Testing ») permet un balayage rapide à haute résolution de grandes zones, mais les sondes à ultrasons multiéléments courantes sont rigides et elles ne peuvent donc pas s’ajuster à la géométrie changeante des composants.
Par conséquent, ce type d’inspection est facilitée et améliorée grâce à une sonde multiélément flexible qui peut s’adapter aux géométries changeantes de sorte que les éléments restent perpendiculaires à la surface tout au long de l’inspection. Cette fonction unique réduit le besoin d’établir des plans d’inspection complexes, augmente la couverture de chaque balayage, simplifie l’interprétation des données et réduit les besoins en équipement requis pour l’inspection.
Créer une nouvelle sonde de conception novatrice
Une première étude a été menée pour analyser les techniques ultrasonores actuelles utilisées pour l’inspection du rayon des composants en CFRP, notamment l’utilisation de sondes monoéléments UT et de sondes d’immersion courbes PA. Les tests ont été réalisés sur un panneau en CFRP présentant deux sections plates et un rayon de 25 mm.
Étape 1 : Validation de la méthode d’inspection actuelle à l'aide d'une sonde UT
La figure 1 montre la sonde UT couplée au rayon et orientée perpendiculairement au rayon intérieur afin de permettre l’observation de la paroi de fond. Notez que l’inspection est très sensible à l’orientation, par conséquent les défauts connus pourraient facilement être manqués par un inspecteur inexpérimenté.
La figure 2 montre le A-scan et le B-scan générés par la sonde, lesquels ont été codés sur la longueur de la pièce. Deux défauts ont été détectés (encerclés en rouge), à l’endroit où la perte de réflexion de la paroi de fond et le réflecteur apparaissent plus proches dans le temps.
Étape 2 : Validation de la méthode d’inspection à l’aide d’une sonde courbe PA
Le test avec la sonde d’immersion courbe PA supposait une configuration et une acquisition de données plus compliquées. Un support de sonde était nécessaire pour positionner mécaniquement la sonde selon une colonne d’eau et une orientation spécifiques par rapport au rayon. La figure 3 montre la configuration avant l’immersion dans un réservoir d’eau.
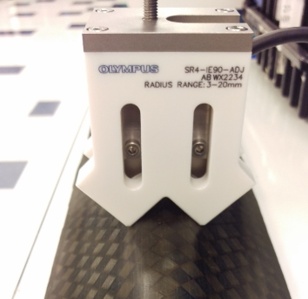
Figure 3 – Sonde courbe concave (3–25 mm) dans un support positionné pour l’inspection du rayon d’un panneau CFRP
La figure 4 montre le A-scan, B-scan et C-scan obtenus avec la sonde courbe concave. Entre autres difficultés propres à la configuration de ce test, on note le choix de la colonne d’eau, la détection de la réflexion de la paroi de fond et le dimensionnement des défauts. Dans la vue B-scan, le réflecteur de 12,7 mm est étiré en fonction de la colonne d’eau et de l’ouverture virtuelle (nombre d’éléments) choisies. La zone de couverture change également de manière significative en fonction de la colonne d’eau, de la profondeur focale et de la taille de l’ouverture.
Conception sur mesure d’une sonde multiélément flexible
Comme expliqué plus haut, lorsque les pièces inspectées présentent une géométrie complexe, il faut utiliser une très petite sonde pour l’inspection de chaque petite section du panneau CFRP à la fois. En s’appuyant sur les résultats d’analyse des méthodes d’inspection avec sonde UT conventionnelle et avec sonde PA courbe, l’équipe a conçu et créé une sonde multiélément flexible permettant une visualisation rapide des zones courbes.
Troisième étape : évaluation de la durabilité de la sonde flexible
Avant d’inspecter les composants en CFRP à l’aide de la sonde multiélément flexible, on en a testé les limites de flexion concave et convexe. Chaque test exigeait de fléchir la sonde autour d’une pièce de diamètre connu, et puis d’en vérifier l’état pour s’assurer qu’elle ne s’était pas endommagée. La figure 5 montre une flexion concave de la sonde autour d’une jauge de 12,7 mm de diamètre sans que des dommages soient causés.
La figure 6 montre une flexion convexe de la sonde (éléments positionnés vers l’extérieur) autour d’une jauge de 40 mm de diamètre sans que des dommages soient causés.
Ces tests ont permis aux ingénieurs de déterminer les limites assurant une utilisation sûre de la sonde flexible. De plus, on a constaté qu’une flexion accentuée de la sonde entraînait une perte de sensibilité des éléments individuels et un déchirement du matériau de la languette.
Étape 4 : validation des résultats d’inspection obtenus avec la sonde flexible
Les tests de résistance à la flexion ont prouvé que la sonde pouvait être utilisée dans sa position fléchie concave sur le diamètre extérieur du rayon de 25 mm d’un composant en CFRP. La figure 7 montre la configuration d’inspection d’un composant en CFRP à l’aide de la sonde flexible maintenue en contact avec le rayon de 25 mm.
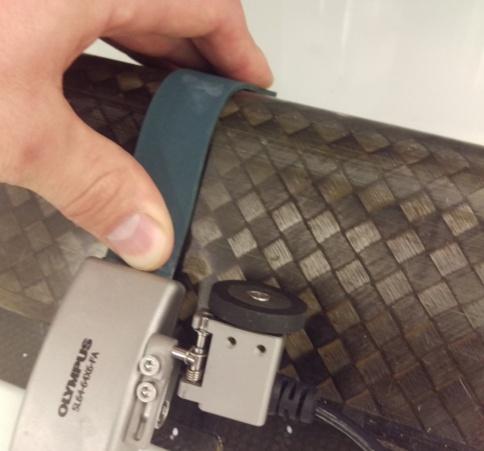
Figure 7 – Sonde flexible couplée aux parties plates et au rayon extérieur de 7 mm d’un composant en CFRP
La figure 8 montre les vues A-scan, B-scan et C-scan des données acoustiques acquises à l’aide de la sonde flexible. Entre autres avantages, ce type d’inspection permet une couverture complète du rayon, des mesures précises des défauts et une configuration mécanique simple. La vue B-scan montre que les résultats pour le réflecteur de 12,7 mm ne sont que légèrement supérieurs à la mesure réelle de 15,9 mm, ce qui s’avère beaucoup plus précis que les résultats obtenus avec la sonde d'immersion concave. La zone de couverture est beaucoup plus grande et les données sont plus faciles à interpréter, car les résultats incluent les données acquises pour la première partie de la face plane, passant par le rayon, jusque dans la seconde partie de la face plane.
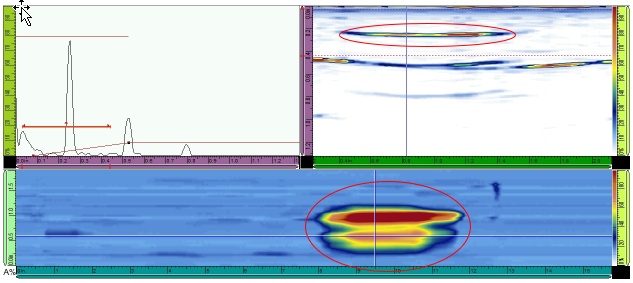
Figure 8 – Vues A-scan, B-scan et C-scan de la sonde multiélément flexible détectant un défaut dans un composant en CFRP
Au-delà de l’inspection des panneaux CFRP
Notre évaluation des trois méthodes d’inspection — avec sonde monoélément UT, avec sonde d'immersion courbe PA et avec sonde multiélément flexible — nous a permis de constater que la sonde flexible est celle qui offre la meilleure facilité d’utilisation et les résultats les plus précis. La sonde multiélément flexible est pratique pour les inspections à faible volume effectuées par contact à l’aide de presque tous les appareils de recherche de défauts Olympus.
Nous avons rapidement constaté les avantages de cette sonde pour d’autres types d’applications, notamment l’inspection des coudes de tuyaux. La capacité de la sonde à générer des données C-scan peut aider les utilisateurs à quantifier rapidement les effets de la corrosion dans une zone donnée, ce qui permet aux clients d’économiser temps et argent.
C’est pourquoi nous avons conçu le scanner FlexoFORM™, lequel intègre une sonde multiélément flexible justement prévue pour l’inspection de la corrosion sur les coudes de tuyaux. Cette solution d’inspection comprend une sonde flexible de 7,5 MHz (64 éléments, pas de 1 mm, élévation de 7 mm) placée dans un sabot à colonne d’eau. Le sabot à colonne d’eau permet un excellent couplage sur les pièces à géométrie complexe et aide à protéger la sonde. Il s’agit d’une solution rapide et économique adaptée à l’inspection des coudes de tuyaux.
Pour le moment, ce sont les seules solutions de notre gamme de produits intégrant les sondes multiéléments flexibles ; toutefois, les nombreuses avenues intéressantes à explorer les placent au premier plan de projets de développement : pièces en CFRP, plastiques (polyéthylène haute densité), et autres types de pièces à géométrie complexe.
Consultez les experts de notre équipe de conception de sondes au sujet de votre application spéciale en remplissant le formulaire Demande de renseignements sur les sondes et les sabots multiéléments personnalisés ou contactez-nous directement.
Contenu connexe
Solutions d’Olympus pour les applications spécialisées
Contactez-nous