Eddy current technology is used to inspect conductive materials to detect discontinuities. Capable of detecting cracks and corrosion, ECT is largely used to verify the integrity of the test object. It can be also used to measure the conductivity of metals and measure the coating and plating thickness.
Compared with other nondestructive testing (NDT) methods, eddy current inspection offers excellent potential for Industry 4.0 adaptation. Because of certain inherent characteristics, ECT technology has been digitized and integrated into in-line robot-based or cobot-based systems. Some of the advantages that make such integration possible include:
- No surface contact or couplant is required, eliminating the risk of damage to the part.
- It’s fast and provides instant results so high-speed inspection is possible.
- Detects through coatings and paint so there is no surface preparation involved.
These reasons are also the main arguments for choosing ECT as an alternative to magnetic particle (MT) and penetrant testing (PT).
Engineering Automated Bolthole Inspection
ECT’s assets make it an easy-to-use and efficient technique for high-speed and demanding production line environments. We’ve also designed inspection equipment specifically for key industrial applications. Bolthole inspection, for one, is an application required both in manufacturing and in-service settings for a wide range of industries, including automotive and aerospace. Bolt holes in components need to be validated for quality control and assurance and maintenance.
We have manufacturer customers that have implemented the NORTEC™ 600 eddy current flaw detector and our optimized ECT bolthole probes and scanners on their production line. The flaw detector’s advanced features make it easy to use and enable integration into automated, remote-controlled, and robotic systems.

Designated Bolthole Scanners for ECT
Eddy current bolthole scanners can be used to detect cracking occurring inside bolt holes. When integrated into an automated in-line system, our eddy current rotating scanners spin the bolthole probe or countersink probe inside the hole while a robotic component, for example, performs automatic indexing. This enables highly efficient inspection of multiple bolt holes in metal parts, helping achieve the targeted production line speeds.
To optimize the system configuration, our scanners come with POWERLINK™ technology that enables the NORTEC 600 software to automatically recognize the model and offer the user predefined setup parameters for the frequency, gain, and filters.
Features of our bolthole scanners:
| ![]() |
Eddy Current Probes for Our Rotating Scanners
Probes for our eddy current rotating scanners are made of plastic or stainless steel. Different sizes are available to fit in the bolt hole under inspection. We also offer countersink probes, which are designed specifically for the inspection of the countersink opening of a bolt hole.
Here are some of the models you can choose from:
Stainless Steel Body![]() | Countersink Probe, Plastic Body![]() |
Plastic Expendable Body![]() | Countersink Probe, Stainless Steel Body![]() |
Adjustable X-Type Body![]() |
Interpreting ECT Results and Setting Alarms
When the eddy current probe detects a crack in a bolt hole, its impedance changes and a signal appears on the eddy current instrument’s impedance plane and strip chart. An alarm box can be set to capture specific variations of the signal. The instrument provides the vertical and horizontal components of the signal through analog outputs on the I/O connector.
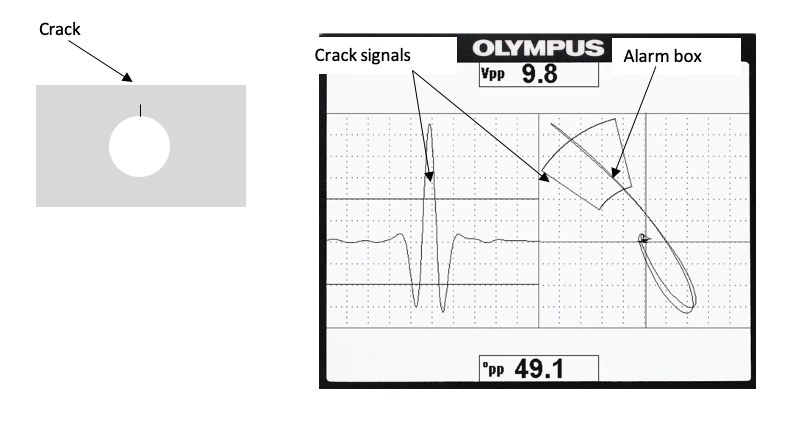
Crack in a bolt hole (left) detected by the eddy current probe and the corresponding signals on the strip chart and impendence plane (right), extending beyond the alarm box tolerance
Automated Solutions―In-Line Robotic Inspection Systems
As shown in the diagram below, it’s possible to engineer a solution that integrates our eddy current equipment and your PC. The PC controls the NORTEC unit, receives the alarm trigger signal, and communicates with and controls a robot or cobot (collaborative robot). Example systems we’ve seen have a robotic arm that is programmed to hold and insert the rotating scanner’s probe into the bolt holes in parts on the production line.
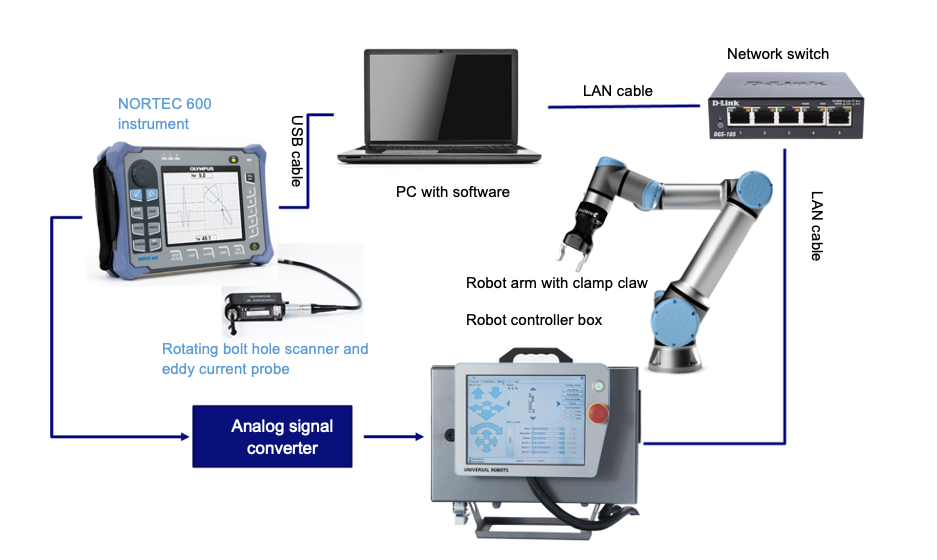
Diagram of a potential robotic inspection solution with the ECT components supplied by Evident labeled in blue
Related Contents
Application Note: Eddy Current Bolthole Inspection Smart Filter Adjustment
Locating Cracks on the Space Station—Eddy Current Flaw Detectors with the Right Stuff
5 Ways to Gain an NDT 4.0 Edge with the X3 Remote Collaboration Service