Comparaison des mesures de propreté des différentes normes
Dans ce quatrième article de cette série en six parties, nous découvrirons comment les niveaux de contamination sont déterminés. Nous discuterons notamment de la définition des codes de propreté et de la vérification par rapport aux valeurs maximales autorisées. Voici comment la détermination du niveau de contamination s’inscrit dans le processus global de contrôle de la propreté des composants :
- Préparation
- Extraction
- Filtration
- Séchage et pesée
- Inspection
- Acquisition d’images
- Détection des particules
- Mesure granulométrique et classification des particules
- Extrapolation et normalisation du nombre de particules
- Détermination du niveau de contamination
- Définition du code de propreté
- Vérification par rapport au maximum autorisé
- Séparation des particules métalliques et non métalliques
- Identification des fibres
- Examen des résultats
- Production de rapports
Détermination du niveau de contamination
Pour la plupart des normes de propreté, un nombre abstrait est indiqué au lieu du nombre réel de particules mesurées (ou extrapolées). Ensuite, le niveau de contamination est vérifié pour chaque classe de tailles de particule. Il s’agit du deuxième niveau de classification, mais cette fois, les particules ne sont pas classées en fonction de leur taille. En effet, les classes sont définies selon le nombre de particules dans la classe. Ces niveaux de contamination permettent une comparaison simple et rapide des différentes mesures de propreté, même si cela est parfois simpliste.
Les niveaux de contamination courants sont définis dans la norme ISO 16232 :
- Niveau 00 : aucune particule sur une surface de 1000 cm2
- Niveau 0 : moins de 1 particule sur une surface de 1000 cm2
- Niveau 1 : plus de 1, mais moins de 2 particules sur une surface de 1000 cm2
- Niveau 12 : plus de 2000, mais moins de 4000 particules sur une surface de 1000 cm2
Ces classes de contamination sont définies pour la plupart des normes internationales. Jusqu’à 26 niveaux distincts peuvent être définis, et ceux-ci seront mesurés pour chaque classe de tailles de particule. Ces niveaux de contamination sont généralement similaires pour chaque classe de tailles (p. ex., pour la norme ISO 16232) (fig. 1), mais ils peuvent être définis différemment pour chaque classe (p. ex., pour la norme SAE AS4059).
Définition du code de propreté
Certaines normes réduisent la représentation des données mesurées pour un produit à une description brève. Ce code de propreté dépend de la norme et est composé des classes de tailles ainsi que des niveaux de contamination des particules trouvées. La figure ci-dessous (fig. 2) présente un exemple de code de propreté selon la norme ISO 16232 (A), qui comprend les étapes suivantes :
- Étape 1 : Détection et mesure des particules
- Étape 2 : Normalisation et classification des particules
- Étape 3 : Vérification du niveau de contamination
Il convient de noter que cette forme de code de propreté concerne uniquement la norme ISO 16232. Les autres normes définissent un code de propreté différent. Le premier « A » indique que la normalisation a été effectuée pour une surface de 1000 cm2 de l’échantillon. Les classes voisines ayant le même niveau de contamination peuvent être combinées.
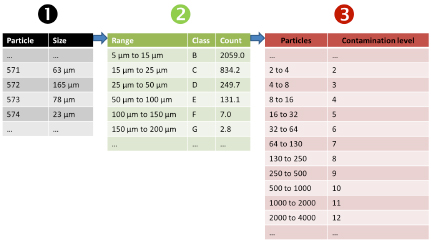
Figure 2 : Exemple de code de propreté selon la norme ISO 16232 (A). Le code de propreté du composant (CCC) qui en résulte pour cet exemple est A (B12/C10/DE8/F3/G2/HIJ00).
Vérification par rapport aux valeurs maximales autorisées
L’objectif réel du contrôle de la propreté est de mesurer la contamination et de décrire les résultats selon la norme sélectionnée. L’approbation et la vérification par rapport à une valeur maximale sont seulement optionnelles et ne font pas toujours partie du processus de contrôle de la propreté.
La limite maximale est définie lors de la configuration de l’inspection. Il peut s’agir du nombre absolu de particules ou d’un code de propreté maximal. Cette valeur est vérifiée lors de l’examen de la membrane du filtre et tout dépassement de la valeur maximale autorisée est indiqué instantanément. Le cas échéant, l’opérateur est libre de cesser complètement le processus de mesure et d’enquêter sur la source de la contamination.
L’exemple suivant (fig. 3), créé à l’aide du logiciel technique de contrôle de la propreté des composants OLYMPUS CIX, montre les résultats de la vérification par rapport aux valeurs maximales autorisées lors de numérisation de la membrane.
![]() | ![]() |
Figure 3 : L’image de gauche représente les résultats pour l’échantillon après 2 minutes de numérisation, avec des niveaux encore acceptables. L’image de droite montre les résultats de la numérisation 2 minutes plus tard. Il y a alors trop de particules dans les classes de taille B, H et I. Par conséquent, l’approbation globale est « NOK » (Not OK).
La prochaine étape du processus est la séparation des particules métalliques et non métalliques et l’identification des fibres. Consultez l’article Identification des fibres et des particules métalliques et non métalliques, le cinquième article de notre série Démystification du processus de contrôle de la propreté des composants.
Contenu connexe
Démystification du processus de contrôle de la propreté des composants – Partie 1
Démystification du processus de contrôle de la propreté des composants – Partie 2
Démystification du processus de contrôle de la propreté des composants – Partie 3