Einführung
In den Bereichen Erdöl- und Erdgasindustrie, Petrochemie und Energieerzeugung kommen häufig dickwandige Komponenten (beispielsweise Rohre) zum Einsatz. Um die Kosten niedrig zu halten, werden diese dicken Komponenten in der Regel aus einfachem Kohlenstoffstahl gefertigt und mit einer Auflage (Verkleidung) aus einer korrosionsbeständigeren Legierung versehen, um die Lebensdauer zu verlängern und die Sicherheit des Systems zu erhöhen. Dieselben korrosionsbeständigen Legierungen können auch als Schweißzusatz verwendet werden, wie bei dem in Abbildung 1 dargestellten Teil. Diese Komponente stammt aus einer Rohrleitung, durch die eine korrosive Chemikalie unter hohem Druck floss, sodass Kohlenstoffstahl allein nicht ausreichte, um über einen längeren Zeitraum der strömenden Flüssigkeit und Korrosion zu widerstehen. Wenn sich das Schweißgut vom Werkstoff eines Bauteils unterscheidet, spricht man von einer „Mischschweißnaht“. Mischschweißnähte sind eine Herausforderung für die zerstörungsfreie Prüfung (ZfP). In der Vergangenheit wurde zur Untersuchung dieser Mischschweißnähte häufig die Durchstrahlungsprüfung verwendet. Dickere Materialien erfordern jedoch wesentlich längere Belichtungszeiten, was die Gesamtdauer und die Gesamtkosten der Durchstrahlungsprüfung erhöht. Diese Schwierigkeiten sowie die Fortschritte auf dem Gebiet der Phased-Array-Technologie machen Ultraschallprüfungen zu einer sinnvollen Alternative für solche Prüfungen. | Abbildung 1: 95 mm dickes Bauteil mit Mischschweißnaht und Auflage |
Herausforderungen bei der Prüfung von Mischschweißnähten und dicken Schweißnähten
Bei dieser Rohrleitungsprüfung gab es zwei große Herausforderungen: das Material der Mischschweißnaht und Auflage sowie die Dicke des Bauteils (95 mm).
Die Prüfung von Mischschweißnähten mit dem konventionellen Transversalwellenverfahren ist schwierig. Wenn ein Ultraschallstrahl eine Komponente mit Schweißnaht durchdringt, können sowohl die metallische Grenzfläche als auch die grobkörnige Struktur der Schweißnaht eine Reflexion (Rückstreuung) und Brechung der Ultraschallwellen verursachen. Dies wiederum führt zu einer Verzerrung, Aufspaltung und Schwächung des Ultraschallstrahls. (Weitere Details finden Sie in dem Anwendungsbeispiel „Einfache Ultraschall-Phased-Array-Prüfung von korrosionsbeständigen Legierungen und Mischschweißnähten“).
Neben den Mischschweißnähten bringen dicke Bauteile spezifische Herausforderungen mit sich. Es muss mehr Energie in das Teil eingeleitet werden, um eine Erkennung mit guter Wahrscheinlichkeit und genaue Messwerte zu erreichen.
Die Lösung: der Dual Linear Phased-Array-Sensor A26
Der DLA-Sensor A26 wurde entwickelt, um Probleme bei der Prüfung von dicken Mischschweißnähten zu lösen. Dieses Sensormodell verwendet niedrige Ultraschallfrequenzen, große Aperturen und das TRL-Verfahren (Senden und Empfangen von Longitudinalwellen). Da es bei Ultraschall-Longitudinalwellen niedriger Frequenzen zu deutlich weniger Verzerrung und Schwächung kommt, eignen sie sich zur Prüfung von Mischschweißnähten besser als Transversalwellen. Die Sender-Empfänger- bzw. Mehrfach-Sensor-Konfiguration ermöglicht es auch, mehr Schallenergie in das dicke Bauteil zu leiten, ohne dass sich damit der Störpegel erhöht.

Abbildung 2: Zeichnung der Schweißfase und des Mischschweißnahtprofils
Aufgrund der Modenumwandlung (von Longitudinal- in Transversalwelle) bei der Reflexion der Welle von einer Oberfläche sind nur Verfahren mit Direkteinschallung praktikabel (Direkteinschallung).
Bei dieser Prüfung bestand das 95 mm dicke Bauteil aus einem Kohlenstoffstahl-Basismaterial mit einer aufgeschweißten 825er Legierung und einer Nickellegierung (ErNiCrMo-3 + ENiCrMo3T1-4) als Schweißzusatz (siehe Abbildung 1). Die Schweißnaht wurde bündig angeschliffen, um eine Prüfung nach möglichen Querfehlern zu ermöglichen (bei 0 Grad und 180 Grad, wie in der in Abbildung 7 gezeigten Prüfebene dargestellt).
Es wurden zwei verschiedene Sensorfrequenzen verwendet. Die Unterseite des Demonstrationsprüfblocks war der relevante Bereich (siehe Abbildung 4). Um Verbindungsfehler an der Seitenwand, die ID-Kerbhöhe und alle Längsfehlerlängen zu bestimmen, wurde zunächst der Phased-Array-Sensor (PA) A26 mit 5 MHz verwendet. Anschließend wurde eine niedrigere Frequenz (Sensor A26 mit 2,25 MHz) verwendet, um die Penetration in die als Zusatzmaterial eingesetzte stärker abschwächende Nickellegierung bei Schrägwinkeln von 0 und 180 Grad zu erreichen (Abbildung 5).
Die Abbildung 7 und 8 zeigen die Querfehler durch die Seitenbohrung mit 5 mm Durchmesser; diese wurden mit dem Sensor A26 bei 2,25 MHz selbst tief in dem dicken Schweißzusatzmaterial präzise erkannt.
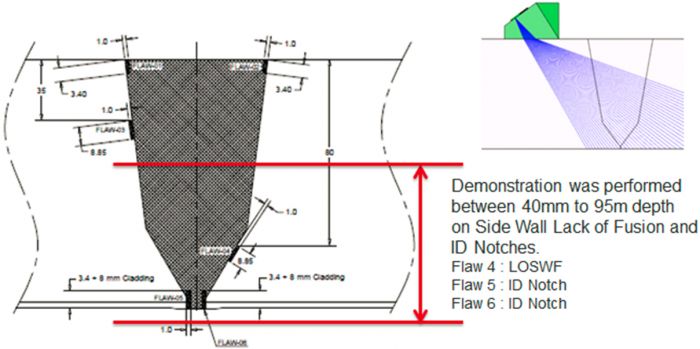
Abbildung 4: Relevanter Bereich dieser Anwendung mit der fehlenden Verbindung der Seitenwand und den ID-Kerben
Vorteile des Einsatzes des DLA-Sensors A26 bei dicken Mischschweißnähten
Mit unseren Dual Matrix Array (DMA) und Dual Linear Array (DLA) Sensoren konnten wir schallstreuende Materialien bzw. Mischschweißnähte gut auflösen. Einige Beispiele für diesen Erfolg finden Sie in den folgenden Anwendungsbeispielen: „Dual Matrix Array Sensoren für die Schweißnahtprüfung schallstreuender Materialien“ und „Prüfung von austenitischen Stahlrohren mit kleinem Durchmesser mittels Dual Linear Array Sensoren (DLA).“ Bestimmte dickwandige Anwendungen stellten jedoch für ältere Sensormodelle immer noch eine Herausforderung dar. Der DLA-Sensor A26 wurde speziell für dicke Komponenten entwickelt. Seine niedrigere Frequenz ermöglicht eine bessere Durchdringung und die Mehrfach-Sensor-Konfiguration und die größere Apertur übertragen mehr Energie in das Bauteil, ohne den Störpegel zu erhöhen.
Abbildung 5: Vergleich der S-Bild-Ergebnisse der Sensoren A17 und A26 bei einem Längsfehler
Abbildung 6: Vergleich der C-Bild-Ergebnisse der Sensoren A17 und A26 bei einem Längsfehler
Fazit
Mit dem neuen Sensor A26 ließen sich die Dimensionen besser bestimmen als mit unseren kleineren Dual Array Sensoren.
Aufgrund der größeren Apertur und der höheren Frequenz des PA-Sensors A26 wurden mit 5 MHz die Verbindungsfehler an der Seitenwand, die ID-Kerbhöhe sowie alle Längsfehlerlängen genauer gemessen als mit dem Sensor A17 bei 2,25 MHz.
Der Sensor A26 mit 2,25 MHz konnte die als Zusatzmaterial eingesetzte Nickellegierung Inconel 825 bei einem Schrägwinkel von 0 Grad und 180 Grad durchdringen.
Abbildung 7: Demonstrationsprüfblock mit Querfehlern (Seitenbohrungen mit 5 mm Durchmesser) in Tiefen von 60 mm, 70 mm und 80 mm. Prüfung mit einem Schrägwinkel von 180 Grad im Zusatzmaterial.
Abbildung 8: Bei sektoraler Prüfung erkannte Seitenbohrungen mit 5 mm Durchmesser in Tiefen von 60 mm, 70 mm und 80 mm.