¿Qué es un lavador de amoniaco?
Los lavadores de amoniaco son usados en la industria de tratamiento químico para retirar vapores dañinos de amoniaco a partir de la corriente de salida del aire de las plantas de tratamiento. Para limpiar el gas de amoniaco a partir del aire, los lavadores de amoniaco aplican agentes químicos, como el ácido sulfúrico diluido.
Puesto que están sujetos a condiciones altamente corrosivas, los lavadores de amoniaco tienen que estar hechos de materiales resistentes a dicha corrosión, como el plástico reforzado con fibras de vidrio (fiberglass reinforced plastic, FRP). El cloro es otro gas corrosivo usado en la industria química. Por tanto, las tuberías y tanques de cloro están hechas en su mayoría de FRP. Este material tiene la ventaja de ser ligero y más resistente a la corrosión que la mayoría de los metales de la serie 300. El plástico reforzado con fibras de vidrio o FRP también es asequible a un menor costo (Esp. coste) que los metales resistentes a la corrosión, como las aleaciones de níquel o titanio.
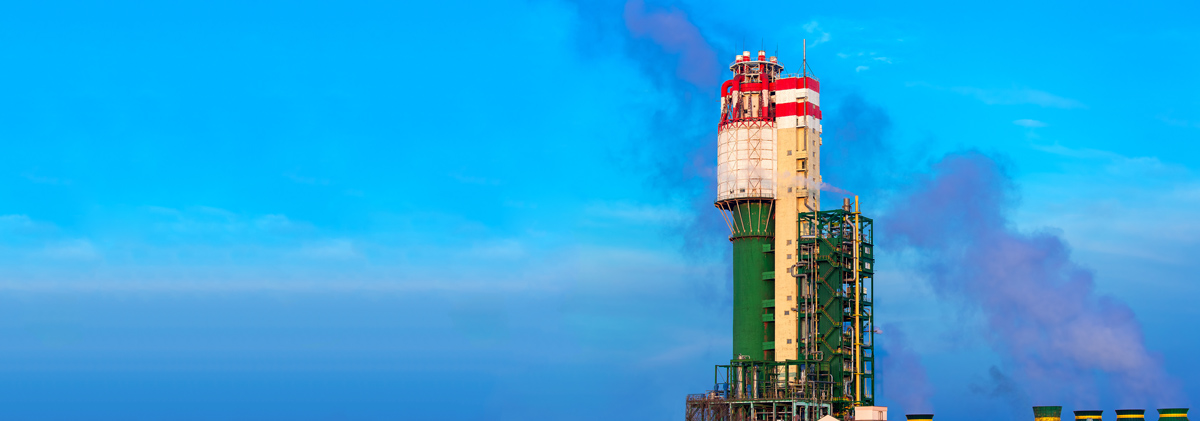
Figura 1. Torre de corriente de salida de una planta de tratamiento químico que produce abono/fertilizante de amoniaco
Desafíos al inspeccionar el material FRP por ultrasonido
Los componentes FRP de los lavadores de amoniaco se usan y desgastan a lo largo del tiempo; su inspección es crucial para los procesadores químicos en una base regular con el fin de evitar fallas en sus sistemas. Es un desafío inspeccionar componentes FRP, como bridas, por medio de los ensayos de ultrasonido convencional (UT), ya que el material atenúa el sonido y la brida presenta una forma irregular.
Solución con el detector de defectos de la serie OmniScan X3 y una sonda DMA
Nuestra solución se compone de una sonda Dual Matrix Array™ (DMA), que permite ejecutar la técnica de ultrasonido multielemento (Phased Array) en modo de emisión-recepción de onda longitudinal (TRL), y el detector de defectos OmniScan™ X3. El uso de este kit, con una configuración que emite haces ultrasónicos de ondas longitudinales de baja frecuencia a partir de un amplio rango de ángulos, hace posible la inspección completa de la parte frontal hermética de estas bridas y del área revestida, susceptible a la corrosión y grietas.
Probar la solución PA Dual Matrix Array de haces angulares
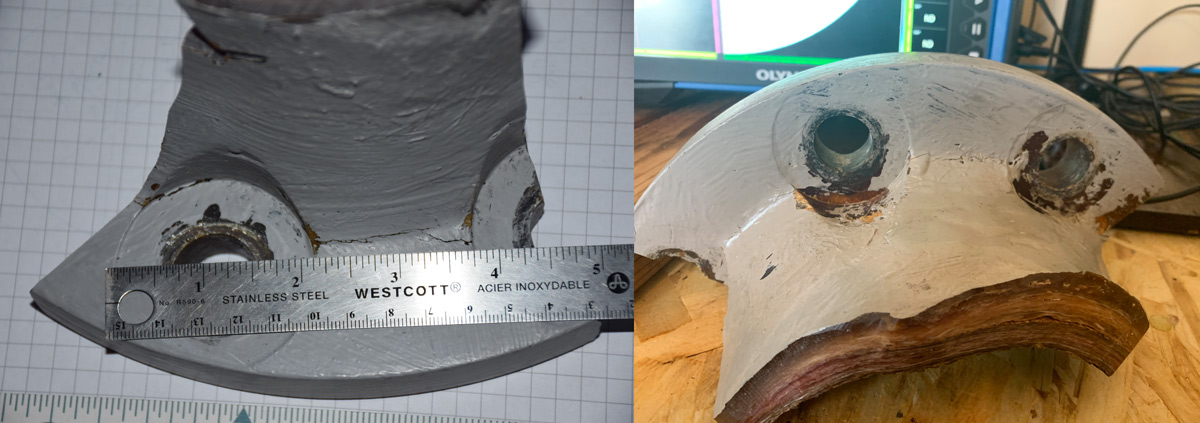
Figura 2. Grieta entre las perforaciones de remaches a partir de un corte de muestra de brida de plástico reforzado con fibra de vidrio
Para probar la eficiencia de nuestra solución, se usaron secciones de una brida FRP dotadas de grietas y corrosión interna (muestra proporcionada por la firma de ingenieros consultores Consultco) [de Figura 2 a Figura 4].

Figura 3. El agrietamiento es visible al usar una fuente de luz en contacto con la muestra.

Figura 4. Condición y corrosión superficial interna del FRP
Las primeras pruebas han demostrado que si bien era posible detectar la corrosión interna con la técnica Phased Array en modo pulso-eco [pulse-echo, P-E], la relación entre la señal y el ruido (SNR) era deficiente para ejecutar una inspección a través de la pieza. El material es muy atenuador y la condición superficial interna se encontraba muy degradada (Figura 4); por tanto, omitir el ultrasonido de fondo a fin de detectar la grieta conectada con la superficie externa fue imposible con la técnica P-E.
La técnica TRL, también conocida simplemente como técnica de emisión y recepción, usa sondas con distintos juegos de emisores y receptores de matriz, como la sonda DMA. Con las sondas DMA, las señales adquiridas se originan sólo a partir del área donde los haces se cruzan entre ellos. Las matrices separadas de emisión y recepción permiten que el tamaño de la suela (zapata) se reduzca, ya que no se requiere ningún material de humedecimiento. Es decir que la sonda está más cerca de la superficie y, por lo tanto, de la región de interés, lo que permite soportar una sensibilidad más alta y evita la atenuación causada por largas trayectorias acústicas en la suela (zapata).

Figura 5. Configuración de inspección que muestra el instrumento y la muestra
El uso de ondas longitudinales en lugar de ondas transversales con la sonda DMA ofrece menos interferencia y una mejor penetración. Esto resulta en una señal de recepción con un nivel de ruido más bajo, lo cual es clave en las inspecciones que implican materiales ruidosos y de grano grueso como el FRP.
Información sobre la sonda y suela (zapata) que se usaron:
Modelo de sonda: Sonda DMA A27
Frecuencia de sonda: 4 MHz
Configuración de elementos: 16 × 2 en cada matriz (matrices de emisión y recepción)
Ángulo de haz nominal refractado de suela (zapata): Onda longitudinal de 55° (OL).
Estrategia de enfoque
En el caso de la inspección y detección de grietas en la superficie, la sonda DMA fue usada (Figura 5) para ejecutar una inspección de ángulo elevado y primer salto. El escaneo sectorial Phased Array fue configurado para incluir ángulos que llegaran tan alto como a los 89 grados. Por encima del ángulo de aproximadamente 78 grados, todos los haces en el A-scan se propagaron de forma paralela a través de la superficie mediante una velocidad longitudinal. Al usar esta técnica de enfoque, fue posible detectar una ranura superficial, grietas y otros defectos.

Figura 6. Detección de la grieta y parte interna de la corrosión de ángulo
Conclusión: Requisitos para una inspección PA exitosa en bridas hechas de FRP
El uso de una configuración de sonda DMA con el OmniScan X3, más la frecuencia de sonda y la estrategia de enfoque adecuadas, hizo que fuera posible detectar las grietas y la corrosión en las bridas hechas de FRP de manera exitosa. Para facilitar el análisis, los datos mostrados (en la Figura 6) se dotan de una superposición personalizada que ha sido diseñada para corresponder con la muestra de brida. De acuerdo con los resultados de escaneo, se pudo detectar y evaluar el daño de la corrosión en el ángulo interno de la brida como también la grieta conectada a la superficie en el componente FRP.